Health and Safety management
Approach
GRI 103-2, 403-1, 403-3As one of the world's largest metallurgical and mining companies EVRAZ is aware of the nature and scale of impact of its activities, considering it a duty to create and maintain safe working conditions for our employees, contractors, and partners. The Company takes a proactive and structured approach in managing occupational health and safety issues, focusing on the ongoing improvement of internal processes, implementing best international practices and instilling safe working methods and safety culture into every employee.
EVRAZ shows an unwavering commitment to follow all legal requirements in its regions of operation as well as internal corporate rules, regulations and standards on health and safety protection that are often even stricter than the rules prescribed by legal bylaws.
The Company operates HSE management system to manage risks in occupational health and safety related to its operational activities. The HSE management system is a set of interrelated actions to help identify potential hazards that may arise during production activities and develop appropriate mitigation measures. It is based on a risk-oriented approach allowing EVRAZ to prevent and avoid cases that could potentially lead to harmful consequences for our employees and contractors.
The basis of EVRAZ HSE management system is the Health, Safety and Environmental Policy, a fundamental document regulating the occupational health and safety issues. The Policy formalises the basic principles that the Group has set for itself as well as the employees’ commitments and expectations in terms of occupational health and safety.
The Company regularly updates, develops, and implements latest HSE regulations and standards containing requirements aimed at ensuring safe conditions and protecting the employees’ at work. All EVRAZ activities are carried out in accordance with the following documents governing the occupational health and safety, and fire safety issues:
- Health, Safety and Environmental Policy.
- Policy Relating to Alcohol, Narcotic Drugs and Tobacco.
- Cardinal Safety Rules.
- Fundamental Environmental Requirements.
- Standard Incident Reporting Rules.
In 2021, a number of corporate HSE documents were revised and amended due to significant changes in occupational health and safety legislation. The changes affected the safety rules for working at heights, operating power units, handling operations and some other areas. In terms of core internal documentation, some changes were made to the Standard Incident Reporting Rules. The Cardinal Safety Rules were also updated and a new lockout, tagout (LOTO) procedure was added that prohibits working without safety locks.
EVRAZ strives to comply with all international standards on occupational health and safety. OHS management system has been adopted at all the Group’s production facilities. The Company is focused on seeing to it that all the Group's enterprises are certified in accordance with the ISO 45001:2018 latest international standard
The Siberia Division that passed the initial ISO 45001 certification in 2020 was subject to inspection control during the reporting period. Its results showed that the declared certification area conforms to the activities carried out by EVRAZ ZSMK, the integrated management system meets the ISO 45001 requirements, is effectively implemented and able to achieve the goals set by the Company's policy.
In 2021, EVRAZ NTMK was certified under ISO 45001:2018 and underwent a supervisory audit as well. The audit results confirmed that EVRAZ NTMK met the requirements of the ISO 45001:2018 international standard, with respective acknowledgement by the Bureau Veritas Certification Rus certification body.
EVRAZ plans to continue certification under
HS initiatives and projects 2021
Risk management
GRI 403–7In the reporting period, the active phase of the Risk Management project was successfully completed. The project is aimed at creating a systematic approach to changing the employees’ attitude to their own safety. It helps to duly identify risks, minimise them, and prioritise budgeting.
At the end of 2021, the project underwent an audit that revealed its strengths and weaknesses. The project assessment showed that the majority of heads of business units considered the project to be an integral part of HSE management systems. We are pleased to see our employees perceive the risk management tools as part of standard daily operations. We regard this as an example of how all the EVRAZ facilities successfully implement the dynamic risk assessment measures.
During the reporting period, EVRAZ trained over 23,000 employees under the Risk Management project. In addition, the employees of the Company’s contracting organisations commenced their risk management training through specially developed internal programmes.
Next year, several processes for working in terms of contractor management are planned to be realised as well. They will be fully integrated into the corporate HSE management system within the implemented project.
Hunt for Risk mobile app
GRI 403–2EVRAZ continued to extensively implement the innovative Hunt for Risk mobile application in the field of occupational safety, that was developed under the Risk Management project. The application helps to identify and eliminate workplace risks in a convenient way, and to increase the level of personnel safety culture. The app functions in two ways: standard – enabling one to record the risks identified by experts in an electronic system, and mobile – providing access to Hunt for Risk on employee’s phones and giving the opportunity to report the risk at any time. Also, all volunteers who have joined the ranks of the Hunters get access to the reward system exchanging the points gained for active use of the application for valuable prizes. In 2021, the Company also rolled out the Hunt for Risk app for the employees of contracting organisations giving them the opportunity to use the app to increase their interest in workplace safety. However, the employees of contracting organisations are not able to use the incentive system as the direct managers of contractors are responsible for their rewards.
Hunt for Risk was originally launched in 2020, and by the end of the reporting period the number of users totalled to 1,280. In 2021, the Company conducted the specialised training that allowed its employees to master simple and comprehensible skills in using the application. As a result of the active implementation of this programme over 70,000 potential hazards were identified in 2021 as such. This indicator exceeded the anticipated result by almost two times, which speaks for the incredible success of the app.
Transformation of HSE processes
In 2021, EVRAZ reviewed a number of its business processes related to occupational health and safety followed by developing the recommendations for their automation and central administration. This coincided with the debureaucratisation initiative carried out earlier on in the Company. The analysis of the existing processes also revealed the need for a revision of the safety management operational model which is scheduled for 2022.
Developing the safety culture
GRI 403-5EVRAZ adheres to its unchanged goal – development and maintenance of an effective safety culture. Our employees can openly discuss all issues related to safety, they also have the right to suspend any operation that represents a potential risk to the occupational health and safety. We are trying to ensure the maximum level of employee engagement, and this has become possible by virtue of the ongoing initiatives in the field of occupational safety, such as the Risk Management project and innovative application for risks identification. These programmes are aimed at encouraging employees to take an increasing interest in their own safety.
During the reporting period, the primary diagnostics and self-diagnostics of the safety culture current status were carried out in the Ural division. According to the results of diagnostics by an independent expert organisation, the safety culture level conforms to the transitional level from the reactive (first) to the dependent (second) level on the Bradley Scale. Based on the diagnostic results, certain recommendations were obtained that will provide for achieving a stable dependent (second) level of safety culture. The Company realises that too fast a pace of change may have the opposite effect, therefore it pays attention to consolidating and maintaining the results achieved.
In the Siberia division in 2021, a self-diagnostics of the safety culture was carried out as well. In the course of it, about 12,000 employees of various workshops were surveyed. The analysis of the answers given to open-ended and closed-ended questions showed that the perception of the safety culture by the employees of the Siberia division was at a stable Dependent level on the Bradley Scale. Moreover, around 90% expressed their satisfaction with the current safety situation. Senior managers expressed particular concern about the safety issues. The conducted self-diagnostics showed not only the existing situation in the division but also identified the key problem areas from the employees’ perspective and, respectively, the areas for development.
Occupational injury prevention
GRI 403–9In carrying out its activities, EVRAZ adheres to its priority of protecting the life and health of employees from harmful and dangerous factors. Despite the tremendous efforts made to achieve this goal, it is impossible to achieve the absolute safety in the real world, therefore, in the process of work the EVRAZ employees and contractors remain exposed to health and safety risks.
In 2021, the following major harmful and dangerous factors that represent the highest danger were identified:
- Moving, rotating equipment, mechanisms and flying objects.
- Hitting by external object.
- Dropped or collapsed objects, materials, etc.
- Fire, flame or smoke exposure.
- Traffic accidents.
- Fall from height.
- Electric shock.
- Exposure to extreme temperatures, and other natural factors.
To reduce potential danger from harmful and dangerous factors of the production environment, EVRAZ conducted an analysis of all production processes. This made it possible to identify all major risk areas subject to development and implementation of technical and organisational measures to reduce harmful impact on the employees. It is also mandatory for all employees of the Group to have all the necessary personal protective equipment (PPE) that can reduce the impact of potentially harmful factors.
The Company actively engages its employees in the process of risk identification and analysis. First of all, this initiative has a positive effect on the safety culture improvement as each and every employee wants to come back home safe and sound and is well aware that employees’ own safety depends on themselves.
To assess the effectiveness of the applied measures of protection against dangerous factors, every year EVRAZ monitors the major safety indicators, including the frequency of time-loss injuries (LTIFR) and the number of deaths. Monitoring these indicators not only helps assess the existing protection measures but also contributes to identifying the areas for development for the next period.
LTIFR
GRI 403–9On an annual basis, EVRAZ carries out assessment of the working conditions at its facilities. The leading indicator reflecting the effectiveness of HSE management systems is the lost-time injury frequency rate (LTIFR). Starting from 2021, the Company has been tracking the indicator values both towards its contractors.
Fatalities
GRI 403–9, SASB EM-MM-320a.1EVRAZ makes every effort to ensure there are no fatalities, yet we regret to report eight fatalities in 2021, including two cases among our contractors.
All accidents in the Company are subject to a mandatory investigation. Prompt identification of critical factors and root causes of incidents helps identify systemic shortcomings and develop the necessary measures to minimise dangerous factors more accurately. The Sustainability Management Committee is responsible for the implementation of such initiatives, both within the Group and in individual divisions. Each initiative implemented by the Sustainability Management Committee is regularly monitored and assessed to determine its effectiveness.
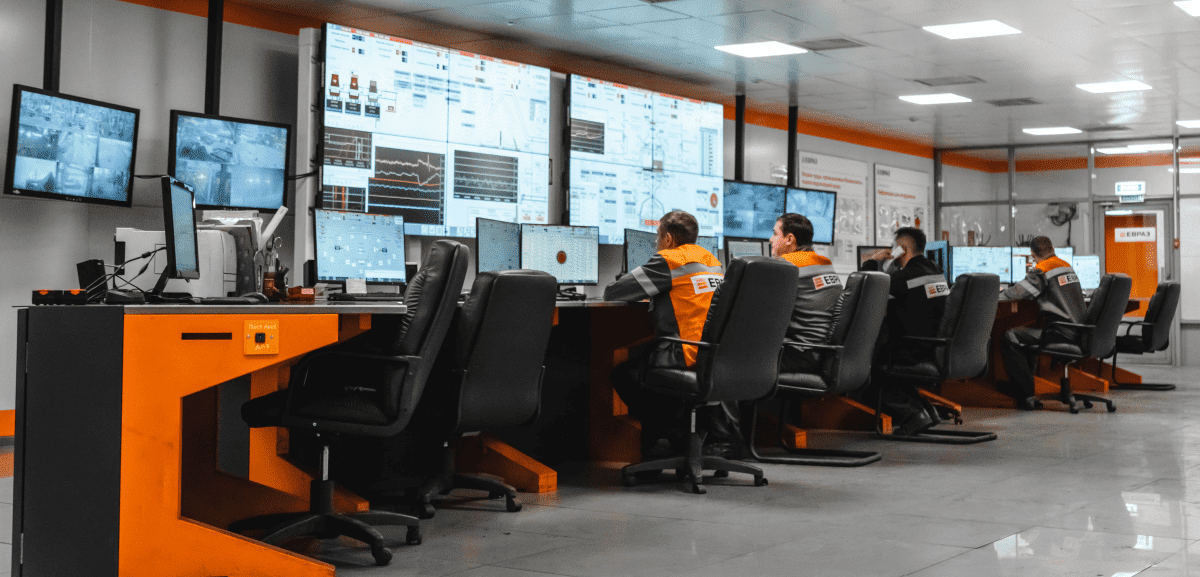
Health protection
To preserve the health of employees, EVRAZ strives to create comfortable working conditions at their workplace. To preserve the health of employees and prevent the occurrence and spread of occupational diseases, the Company conducts all types of medical examinations: mandatory preliminary examinations - upon admission to work, and periodic medical examinations - for employees engaged in work with harmful and (or) dangerous working conditions. EVRAZ also provides employees with the means of individual and collective protection that contribute to the prevention of exceeding the permissible threshold values of harmful factors at workplace.
On an annual basis, EVRAZ monitors the statistics of occupational diseases occurrence. 172 cases of occupational diseases were documented during 2021 at EVRAZ facilities, which was 1.7% lower than in 2020, which saw 175 cases. The structure of registered occupational diseases suffered no changes during the reporting period. Most frequent types of occupational diseases for 2021 are:
- Diseases of the hearing organs (49%)
- Diseases of the musculoskeletal system (39%)
- Respiratory diseases (12%)
The Company has the occupational disease prevention programmes that minimise the risks to the employees’ health. Most programmes are aimed at preventing diseases of the hearing organs and musculoskeletal system as it is these diseases caused by difficult working conditions that occur most frequently with workers.
According to Russian legislation and best international practices of the world community, EVRAZ has arranged insurance against industrial injuries and diseases for all its employees. In the case of detecting any disease resulted from the exposure to harmful or dangerous factors in the working environment, EVRAZ covers all costs incurred in disease treatment, and an employee receives a compensation for his temporary disability. Moreover, the Company provides additional financial assistance to its employees, depending on their personal circumstances and health status.
Transport safety
EVRAZ uses many vehicles in its activities. These are used not only for the Company's operational activities but also for the employees’ transportation. In this regard, EVRAZ pays great attention to the transport safety. We continually carry out modernisation and replacement of the vehicles, and all our employees comply with the transport safety regulations in effect.
In 2021, EVRAZ carried out the modernisation of its railway transport, that is over 10 km of railway tracks, switches and wagons underwent major repairs. In addition, there was accomplished the final stage of the construction of an automatic train approaching notification system for the personnel operating the railway tracks. The Company also updated its fleet of diesel locomotives, repairing the existing ones and purchasing new diesel locomotives and traction units.
In addition to the rail transport, a number of initiatives aimed at improving the road transport safety were implemented in 2021. A training stand was purchased in the Siberia division as a head-on collision simulator that is designated for conducting training tests for all drivers. A new brake stand was installed at EVRAZ KGOK at the technical inspection point to check the braking systems of cars. To improve the transport safety, certain specialised classes were held with drivers under the "Road Safety" programme, and there was arranged a meeting with the traffic police inspectors who conducted a seminar on the road rules changes.
In 2021, EVRAZ carried out a number of planned overhauls of transport, purchased new comfortable buses and automobiles, and equipped a number of its vehicles with tachograph control.
Contractor engagement
Contractors play an important role in ensuring EVRAZ’s day-to-day activities., therefore their skills and competencies are of key importance for providing for the overall safety. The Company has developed a management manual for contractors that sets requirements to their work.
Every year EVRAZ endeavours to more and more involve its contractors in the HSE-related issues. In the reporting period, the Company commenced additional training in risk management project tools for its contractors. The training is planned to be continued and expanded in 2022. In addition, the contractors were provided with an access to the Hunt for Risk application in demo mode. The application enables the contractors to independently record the risks identified during work, thereby increasing a personal interest in ensuring the safe working conditions.
Another innovation during the reporting period was that the Company included its contractors in the LTIFR indicator for the first time.
Emergency prevention and response
All the EVRAZ facilities are equipped with modern means of responding to various emergencies. The Company complies with all the requirements of the national legislation and sees to it that all the facilities have their approved action plans for the localisation and elimination of the consequences of accidents, as well as contemporary warning systems that, when appropriate, send sound alerts across the facility and transmit an emergency signal to a district duty station to warn residents and authorities as along with specialised rescue services.
EVRAZ regularly conducts trainings and emergency drills in accordance with the elaborated emergency response plans. The Company is interested in ensuring that its employees are always appropriately prepared for any emergency situations.
In 2021, the Company directed its special focus on mine and underground mining, hence a quarterly rating of mines in terms of their readiness for emergency situations was compiled.
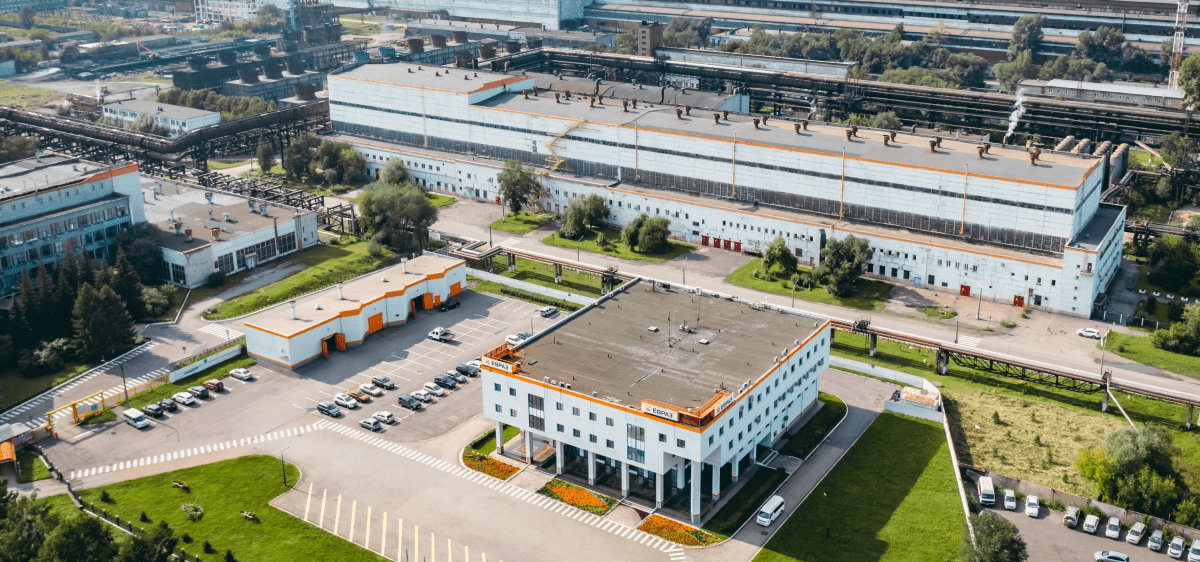