Boosting energy efficiency
GRI 103-2Boosting energy efficiency is a key focus of the Group’s decarbonisation efforts. Energy effective technologies require fewer resources and produce less greenhouse gas emissions. EVRAZ uses modern technologies and modernises equipment to improve energy efficiency and cut the emissions and operational costs.
EVRAZ has a comprehensive system of energy consumption and energy efficiency management. The energy management system of the Urals and Siberia Divisions’ enterprises is certified for compliance with the international standard ISO 50001:2018 by an independent company Bureau Veritas. The Group regularly conducts internal audits of the energy management system of plants and production workshops using a uniform methodology developed based on the requirements and recommendations of the ISO 50001 standard. Internal audits allow enterprises to prepare for external supervisory and recertification audits in compliance with ISO 50001.
The Group seeks to improve the efficiency of its energy management structure and maximise the involvement of employees from both the energy shops (energy generation and distribution) and the production shops (energy consumption). The Urals and Siberia Divisions are characterised by the presence of the Energy Managers. The Group has a position of Energy Efficiency Business Process Development Manager. Teams of experts in the energy management system trained according to the
In 2021 EVRAZ developed a set of internal documents in energy saving and energy efficiency:
- The Group drafted a special standard for energy-efficient design of production facilities and will launch the process of its implementation in 2022.
- In 2021, the Group developed and approved a policy for the use of energy-efficient power distribution transformers. The policy contains energy efficiency criteria to be considered by EVRAZ’s enterprises when purchasing transformers.
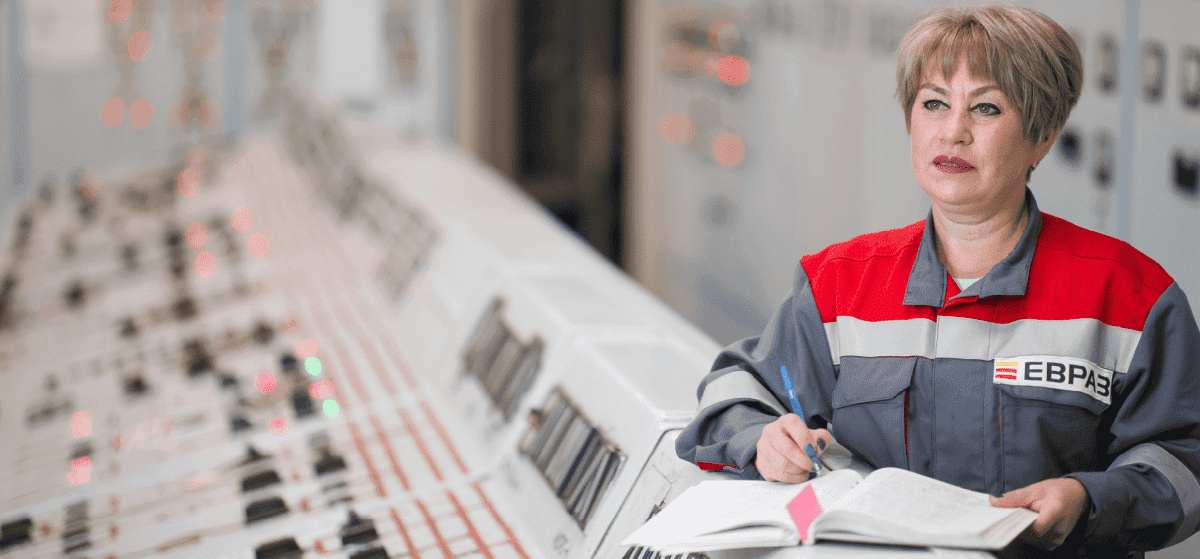
EVRAZ employees participate in special events, such as the Idea Factory, where workers can propose their projects and improvements. The best ideas are implemented. One more activity is the New EVRAZ Leaders project, which allows workers to improve operational processes by researching and adopting their innovations.
Every year the Group holds Growth Points activity, which focuses on energy efficiency issues. During this activity the employees of divisions can offer innovative ideas to enhance the efficiency of production processes. In 2021, the topic of discussion was the production of green steel. The participants proposed to consider the possibility of direct reduction technology usage at the sites. Another exciting concept suggested is to decrease the usage of carbon-containing materials, for instance, in charges. The orginizers of the Growth Points have processed all the ideas and presented the green steel development concept to the Group CEO.
In the reporting year, teamwork based on the Energy Management Platform in accordance with the Production Energy Efficiency Programme was carried out in the divisions. In 2021, the staff responsible for energy management completed training in Energy Transition 4.0. The workers learned about key technical elements of energy transition, possible future scenarios of development and use of renewable energy. Preparing for ISO 50001 certification, employees completed an educational programme according to this standard.
EVRAZ aims to reduce the energy intensity of steel production by 20% by 2025 compared to 2018. This goal is planned to be achieved through the implementation of measures of the five-year energy efficiency programmes at the enterprises. Initiatives of these programmes are aimed to:
and
An important focus area for EVRAZ is accounting of energy resources within the workshops. In 2021, the level of unaccounted energy consumption was lowered, with unmetered inter-shop energy flows reduced from 25% to 15% – this helped to take account of energy consumption in a more proper manner and to minimise energy losses.
In 2021, the total energy consumption of the Group reduced by 2.0% compared to 2020. The reduction resulted from the effective energy efficiency policy. Total energy consumption in the reporting year was 350.8 million GJ. The share of purchased electricity in total energy consumption was 6.3%.
Energy consumption in million kWh: 96,212 in 2019; 89,661 in 2020; 88,324 in 2021.
The data on total energy consumption (steelmaking operations and production) for 2019–2020 was recalculated due to clarification of energy consumption
by NA EVRAZ Inc. and EVRAZ Inc. NA Canada
Energy consumption in million kWh: 9,079 in 2019; 8,852 in 2020; 9,134 in 2021.
Energy intensity of EVRAZ in kWh/tcs: 6,929 in 2019; 6,542 in 2020: 6,469 in 2021. Energy intensity of EVRAZ NTMK and ZSMK in kWh/tcs: 7,655 in 2019; 7,114 in 2020; 7,182 in 2021.
Steel segment
The Group successfully passed certification procedures in compliance with ISO 50001 requirements for EVRAZ ZSMK. Experts commended the level of implementation of the energy management system at the plant. The energy management system was implemented at EVRAZ ZSMK in 2019, and this measure had a tangible economic effect — more than one billion roubles were saved. EVRAZ NTMK and EVRAZ KGOK also showed compliance with ISO 50001. The auditors noted the competent organisational management structure and the availability of all the necessary documents. Due to the effective management system, plants achieved cost savings in energy procurement.
At EVRAZ NTMK, numerous measures were taken to reduce energy consumption.
For example, communication feeders were replaced, the lighting system was modernised (a notable result is a reduction in energy consumption for crane lighting by replacing the light source). NTMK also started to use one pump instead of two to supply water to the heat exchangers. A frequency inverter was installed on the electric motors — this reduced electricity consumption of pumping units.
EVRAZ NTMK uses secondary sources to generate electricity. The construction of a gas top pressure recovery turbine has been completed in 2021. The turbine is fully automated and hardly requires human intervention. This measure will allow NTMK to improve energy efficiency by increasing generation of its own electricity with reducing on the same amount purchased electricity
There were also many technical innovations at EVRAZ ZSMK in the reporting year. The productivity of a coke oven battery was increased. Oxygen consumption on the converter was decreased. The heating system was switched from steam to hot water.
At EVRAZ ZSMK, modern oxygen production facilities built according to international environmental standards were put into operation. The energy efficiency of modern equipment is 30% higher than the efficiency of the equipment used in the oxygen production before. EVRAZ ZSMK also developed a system for automatic control of energy consumption, which allows to quickly obtain data on the power consumption of the aggregate and to adjust its operation.
The specialists of EVRAZ KGOK focused on equipment modernisation. Measures implemented by EVRAZ KGOK in 2021 are mainly aimed at reducing the volume of purchased electricity and natural gas (for example, in 2021, ventilators were upgraded, highly efficient separators were put into operation, incandescent lamps were replaced with LED). EVRAZ KGOK also carried out a series of initiatives in the area of digital transformation of energy supply systems, which made it possible to reduce the volume of energy consumption and obtain significant savings in energy costs. Among the activities performed in this direction, there are optimisation of pump control, optimisation of dredge pump operation mode, introduction of the Advanced Analytics project. Other notable energysaving activities taken by EVRAZ KGOK during the reporting period include increasing power generation, reducing pump running time in winter, and replacing the existing fleet of locomotives with more efficient ones.
Blast furnace gas, coke oven and natural gases, as well as solid fuel, are burned in the steam-blowing power plant at EVRAZ ZSMK. The proportion of natural gas used as fuel balance is 27%, and there is an ambitious target to reduce natural gas consumption to zero.
When the blast furnace gas is supplied, the volume of flue gases increases, so that they should be removed from the boiler. To operate the boiler in gas mode, bypass flue gas ducts were installed on five boilers. The bypass flue gas ducts direct the flue gases through scrubber units and allow for additional blast furnace gas supply.
Power engineers replaced old air heaters with new ones, that helped to increase the use of blast furnace gas by an average of 11 thousand cubic meters per hour. In the future, it is planned to reconstruct all boilers to increase the combustion of blast furnace gas to 100 thousand cubic meters per hour.
Coal segment
In 2021 Raspadskaya Coal Company implemented a number of significant initiatives to optimise energy consumption. The system of technical electricity accounting was installed at Osinnikovskaya mine with the specialists turning off auxiliary power units during periods of the highest cost of kilowatthours. It allows energy consumption to be managed more efficiently. The operating modes of drainage systems were also optimised.
At Raspadskaya mine, a reactive power compensation device was replaced to reduce energy consumption. This measure was taken to minimise energy losses. An important achievement of the reporting year was the recovery of the full operability of reactive power compensation devices at Erunakovskaya-VIII mine. Additional 19 actions to reduce energy consumption or installed equipment capacity were taken by Raspadskaya Coal Company, that saved US$0.6 million in energy costs and reduced energy consumption by 47.1 thousand GJ. Also, five initiatives were carried out to install frequency control systems or soft starter systems for electric motors, resulting in cumulative effects of US$0.2 million and 15.3 thousand GJ.
Steel, North America segment
EVRAZ Pueblo purchases renewable energy from Bighorn solar power plant, which is the project of Lightsource BP company. The plant capacity is 300 MW, and there are 750 thousand solar panels in the territory. EVRAZ Pueblo intends to be the largest consumer of solar energy produced by the company.
EVRAZ Pueblo uses an electric furnace for steelmaking. The products are manufactured in line with the global low-carbon agenda. EVRAZ Pueblo has a challenging goal to become one of the most environmentally friendly steel producers in the world.